CONSTRUCTION PERLITE
PERLITE IN THERMAL INSULATION MORTAR AND PLASTERS
Thanks to the pores in its perlite structure, it has extraordinary heat and sound insulation properties. In buildings; Perlite is used to provide heat and sound insulation between plaster, screed, roof covering and floors. It protects against earthquakes by reducing the dead load of the building due to its light weight. Since it is an inorganic substance, it does not lose its properties at high temperatures and prevents the fire from spreading and dispersing.
Main Usage Areas;
Perlite plasters
Lightweight insulation concrete with perlite aggregate (with cement or gypsum binder)
Lightweight construction elements with perlite aggregate
Perliteuse as heat and sound insulating loose filling material
Perlite use as heat and sound insulator in surface floors
Special purpose perlite concrete made with binders other than cement and gypsum .
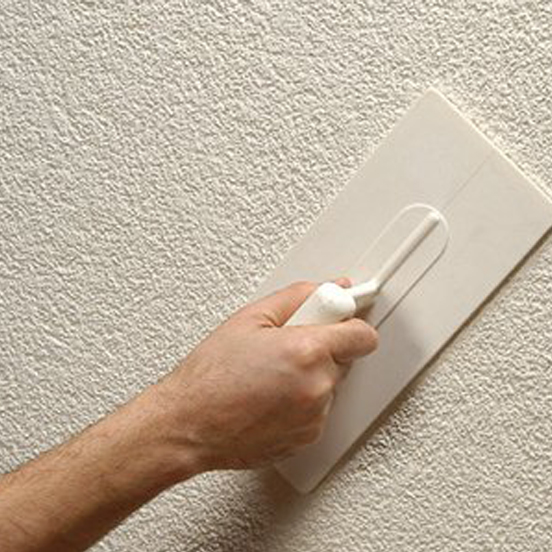
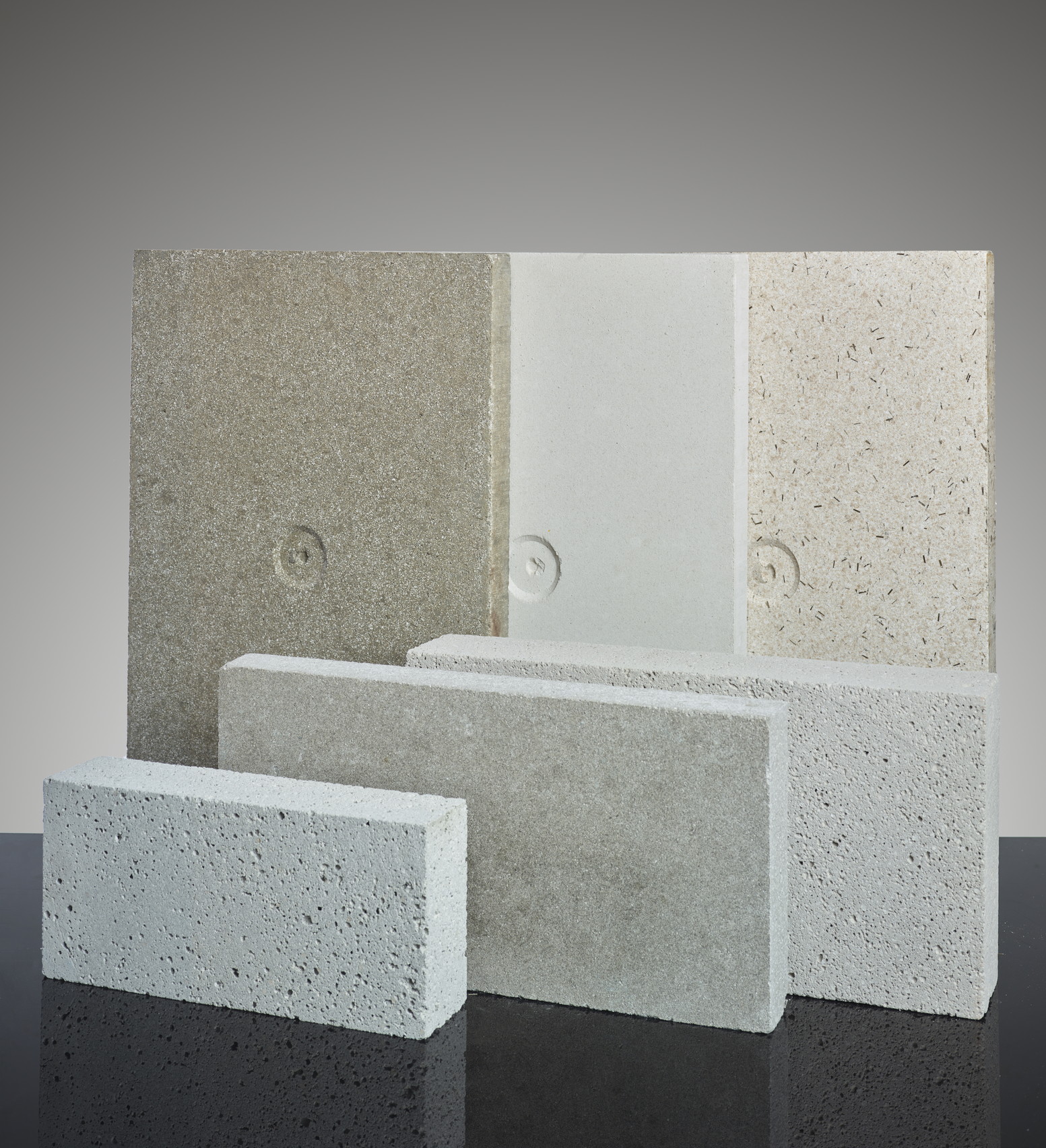
PERLITE IN REFRACTORY BRICK PRODUCTION
Perlite is used as an additive in the production of bricks and mortars used in boilers, annealing-forging, heat treatment and melting furnaces exposed to high temperatures. Refractory blocks and bricks produced by bonding perlite with clay or calcium cement are light and provide high insulation, thus saving fuel.
Main Usage Areas;
Perlite refractory bricks with ceramic binder,
Perlite refractory bricks or concrete with aluminum phosphate binder
Perlite refractory mortar
PERLITE THERMAL INSULATION MORTARS APPLIED ON HORIZONTAL SURFACES
The surfaces on which perlite mortar will be laid should be cleared of loose materials (mortar waste and debris) that are not attached to the roof or floor surface. The application area should be wetted. Perlite mortar is laid between the boards not exceeding 3 – 3.5 m by screeding, compacted and the surface is polished with a trowel or wooden loam. Compaction should not be done with a bottling or surface vibrator. Our applied perlite mortar should be watered for the first 3 days for a good result and after 10-14 days, our perlite mortar will be ready to be covered with waterproofing membranes.
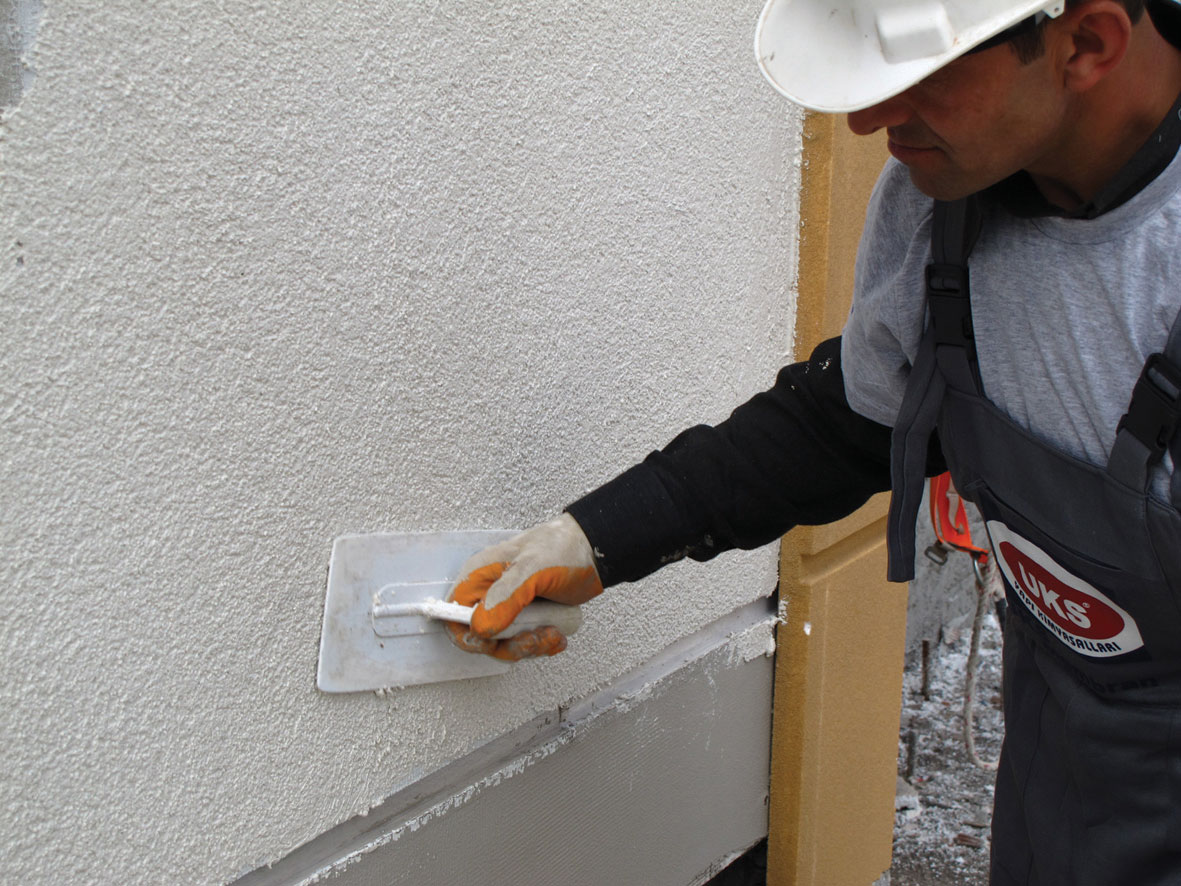
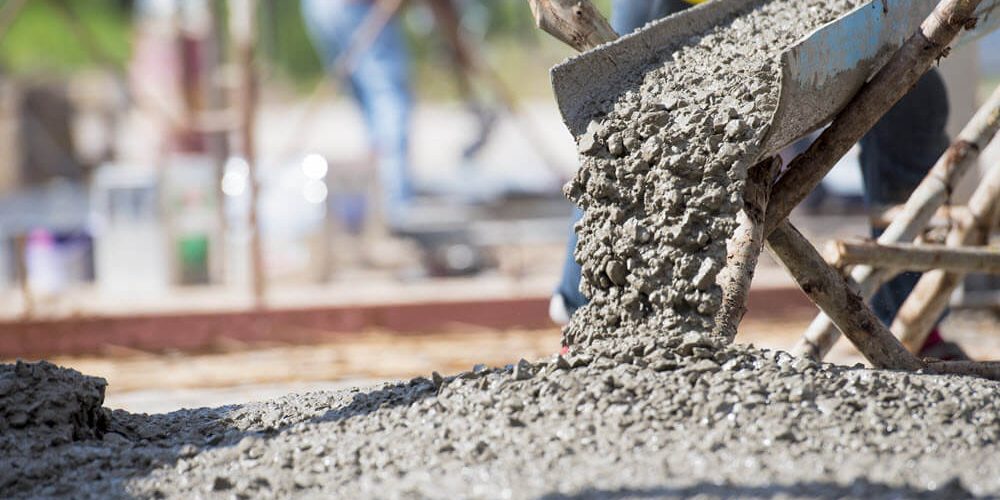
PERLITE THERMAL INSULATION MORTARS APPLIED ON VERTICAL SURFACES
The surfaces on which perlite mortar will be laid should be cleared of loose materials (mortar waste and debris) that are not attached to the roof or floor surface. Before plastering, sand cement grout should be applied on Ytong exposed concrete surfaces. The prepared Perlite mortar should be applied in a single layer by hitting it from bottom to top. The first layer is leveled with a thickness of 1-1,5 cm. After this layer dries, a second layer can be applied to obtain a thicker plaster. It is necessary to irrigate for 3 days for the outlet.
MIXING METHOD:
The mixing ratio of perlite mortars and plasters should not exceed 200 kg/m3 as cement. In practice, this ratio is obtained by mixing 300 liters of Perlite (3 bags) with 1 bag of cement (50 kg).
* 65-70 lt water to the concrete mixer (adjusted not to exceed 300 lt for 1 m3 of mix.)
* 1 bag (50 kg) of np cement is added to form a sherbet.
* 3 Bags (300 lt) of Perlite is added and mixed until a homogeneous mixture is obtained.
* Even if the mixture looks dry, the water ratio should not exceed the given amounts. As a result, when the mixture reaches a plastic consistency after mixing enough, Perlite Plaster is ready for application. (There will be a 5-10 cm collapse in this process.)
* If desired, 10% of natural sand can be added to the mixture at the last stage.
* In practice, a loss of 15-20% may occur due to perlite.
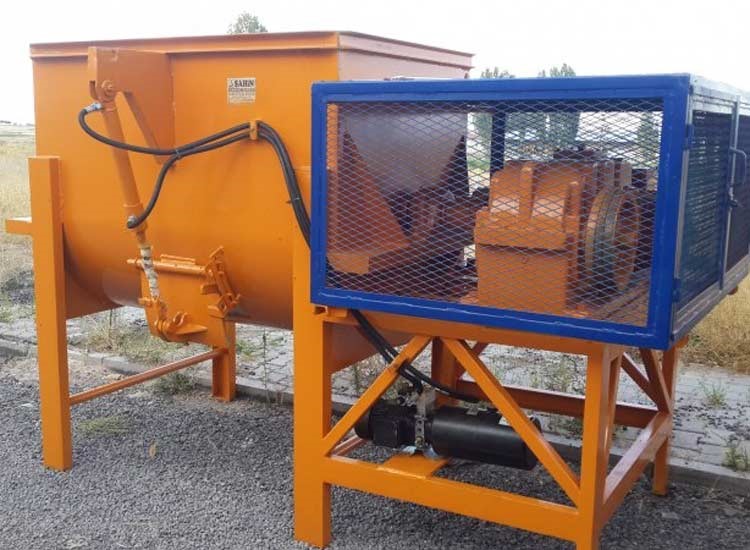
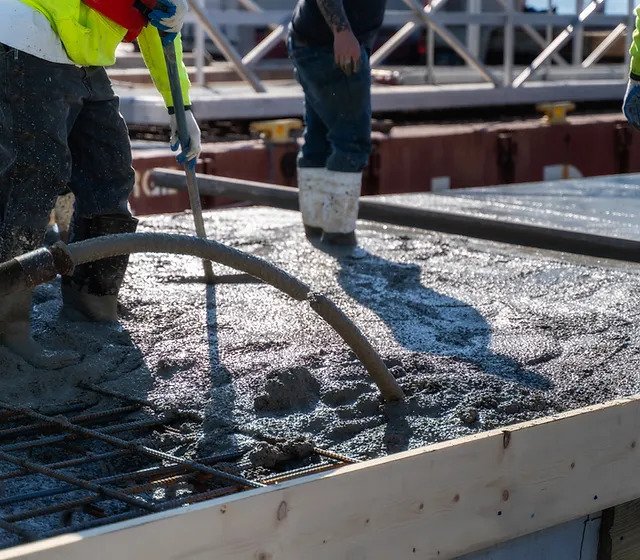
OTHER AREA OF USAGE
By preventing water loss by evaporation in dam lakes, cities and open water reservoirs,
It is used as an insulation layer in vibratory fixing,
Especially in steel constructions against fire.
Perlite is used as an additive in the ceramic and glass industry , in drilling as
additive that facilitates the cementing process.